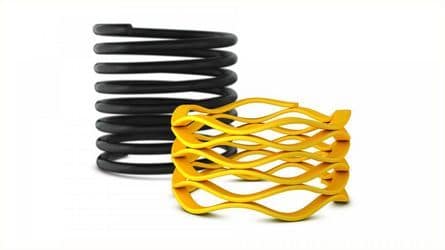
- Wave springs reduce spring height by 50%
- Same force and deflection as ordinary coil / compression springs
- Wave springs fit tight radial and axial spaces
- Over 4,000 standard springs in carbon and stainless steel (¼” to 16″, 6 mm to 400 mm diameters)
- No Tooling Charges on custom designs (.200″ to 120″, 5 mm to 3000 mm diameters)
- Exotic alloys available
Simple ‘wave’ or ‘spring’ washers, as they are commonly known, are traditionally manufactured by die-stamping from annealed sheet metal and then hardened by an austempering process. They are formed using bespoke tooling in an irregular shape so that, when loaded, they act like a spring, deflecting and providing a pre-load between two surfaces. This characteristic can be used to pre-load shafts or bearings, absorb shock, or compensate for dimensional variations.
This type of wave washer has been used worldwide for almost a century and will continue to be in demand where non-critical control of load and space restriction is not an issue. However modern enhanced quality standards and the onward march towards a more compact and lighter end-product means that today™s designers are demanding ever increasing levels of load control and tighter space envelopes in which the springs must operate. Traditional die-stamped methods of manufacture cannot reliably offer these features, however, TFC’s Smalley edge wound wave springs can provide the solution.
Manufactured from flattened round wire and edge coiled to exact specifications, Smalley Single Turn Wave Springs are made with either a GAP or OVERLAP end configuration. These two types of design permit radial expansion or growth in diameter within a cavity, without the binding or hang-up normally associated with die stamped wave washers. Just as their terms imply, the gap type is split to retain a gap between the ends; while the overlap type has overlapping ends. Thus, the ends are free to move circumferentially as the spring outside diameter grows during compression. Also, since they are cold-rolled and, unlike a die-stamped product that requires heat treatment after manufacture, a greater control of spring force is achieved.
Another significant advantage offered by the edge-coiling process is that there is no costly tooling involved therefore, bespoke designs can be produced, as quickly as a standard product, in economic prototype batches with a diameter range from 5mm to over 2000mm. If necessary, the spring design can be altered, with minimal cost, to provide the exact specification without the need for any compromise on the part of the customer.
Variations on a Theme
Utilising the same edge-winding technique enables several innovative spring types to be available.
CREST-TO-CREST® WAVE SPRINGS
Crest-to-Crest® Wave Springs essentially pre-stack the springs in series, this decreases the spring rate proportionally to the number of turns. Uses are typically applications requiring low-medium spring rates and large deflections with low-medium forces.
Traditionally, when a low working height compression spring like this was required, it was necessary to physically assemble a series of single die stamped wave washers by welding or riveting at the wave peaks or by inserting a shim between individual springs to form a stack.
Since Smalley Crest-to-Crest® Wave Springs are manufactured with a single filament of wire, the spring is integrally formed and the wave peaks hold their configuration without the need for such costly and unreliable processes.
As a replacement for helical compression springs, Crest-to-Crest® springs can develop similar forces, yet occupy one-half or less the axial space. This allows for strict space constraints. Crest-to-Crest® Wave Springs will maintain the same force and load specifications of a conventional round wire spring, but with the advantages of lower operating heights, free heights and solid heights.
Crest-to-Crest® Wave Springs are also available with squared-shim ends. Shim ends provide a 360° contact surface when compared to the wave point contact of plain ends. The shim-ends under load, more evenly distribute the springs force upon adjacent components. This feature is similar to the concept of double-disc grinding springs for a flat surface. Shim ends have also been used to affix springs to mating components, as a flat locating surface that may be attached by various methods in the assembly.
INTERLACED WAVE SPRINGS
An Interlaced Crest-to-Crest® Wave Spring is formed from two or three constituent wave springs of similar thickness, amplitude and frequency. The constituent wave springs are wound together to interlace them so that the turns of each spring align each other for the entire length of the interlaced spring. This interlacing effectively increases the thickness of each turn to provide increased loading whilst maintaining similar deflection characteristics.
NESTED WAVE SPRINGS
Nested Wave Springs are pre-stacked in parallel from one continuous filament of flat wire. The need to stack individual springs for higher loads is no longer necessary.
Nested springs result in a spring rate that increases proportionately to the number of turns. They can exert tremendous forces, yet maintain the precision of a circular-grain wave spring. In many applications, Nested Wave Springs replace Belleville Springs, particularly in cases where radial space is tight and accurate force is needed.
Conclusion
To summarise, TFC’s Smalley flat wire wave spring technology offers significant technical and cost-saving advantages over conventional die-stamped and round wire coiling methods of manufacture.
- No tooling required
- Modification to design is immediate and requires no compromise from the customer
- Greater control of specified loading at stated working heights
- No heat treatment
- Size range is almost infinite from 5mm to over 2000mm
- Wide range of material sections and material types
- Short lead times
- Single turn and multi turn types readily available to cater for a broad range of applications
Latest News From TFC
Catch up on all of the latest supply chain, fastener industry and company news from TFC Ltd.
Catch up on all of the latest supply chain, fastener industry and company news from TFC Ltd.