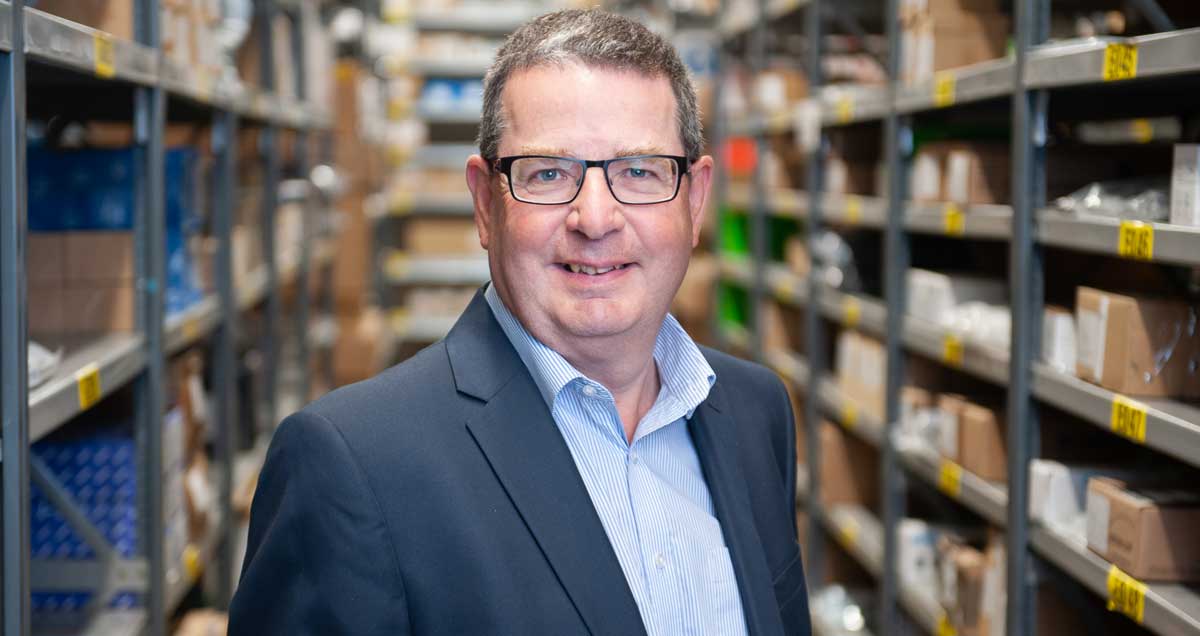
Avoiding long lead times with careful planning
According to Next Green Car, 2021 saw the largest ever annual increase in the number of electric vehicle registrations. Over 305,000 were registered, a 74 per cent increase compared with 2020. Here Simon Ward, technical manager at TFC, shares three ways EV manufacturers can stay ahead of the demand curve.
In 2021, the Government brought forward its ban on new petrol and diesel vehicles from 2040 to 2030. This target has accelerated the EV market boom, creating pressure on design teams to deliver innovation, and impetus on production teams to maximise capacity. So, what can design teams do to stay ahead of consumer demand?
Coping with increased rotational requirements
Drive systems for EVs typically have much higher rotational capacity requirements than internal combustion engine vehicles (ICEs) — 15,000 revolutions per minute (rpm) or more. These applications where high rpm is integral to a product’s function can pose design challenges, because traditional retaining rings fitted on rotating shafts are limited by centrifugal forces and can yield during installation due to the component’s heavy cross-section. Higher rpm risks the centrifugal forces becoming great enough to expand and lift the retaining ring from the groove, causing assembly failure at high speed.
Options to reduce this risk include adding wire ties through the holes of the circlip, or using an additional component to captivate the outside diameter and thus prevent ring expansion. However, these approaches can increase assembly time, weight and add significant additional costs to the finished product.
EV manufacturers can face this challenge head on by specifying technical components designed specifically for high rpm. Smalley Revolox™ Self-Locking Retaining Rings, for example, have a ‘dimple and slot’ design that means that after installation, the dimple is trapped in the slot and the ring locks into place. As the ring rotates it expands, engaging the dimple and slot mechanism and preventing any further expansion. Compared with non-locking alternatives, this offers a much higher rpm capacity.
Dealing with additional connectors
Another challenge is that EVs can have around double the number of fluid connectors of a traditional vehicle. EV batteries, for example, need additional cooling systems to regulate temperature, which increases connector requirements. Design engineers require connectors that can fit in tight spaces and withstand the temperature and pressure conditions.
As well as impacting the design, the requirement for additional connectors can increase time spent during assembly, making it more difficult to keep up with demand. To combat this, design engineers can specify specialised components. ARaymond recently released a range of VDA LOW PUSH Quick Connectors™, which can reduce the insertion force required by 45 per cent compared with other industry standard components with end piece dimensions of NW16. This means only around half the daily effort is required by staff — six tonnes rather than twelve for 1,500 connections a day. This helps create a healthier, happier workforce while also speeding up production.
Staying ahead of the supply chain crisis
Considering the supply chain at the design stage will help your colleagues in production greatly. The current market has created a shortage in a variety of raw materials, particularly steel, causing supply challenges and long lead times, which in some cases are upwards of six months. Researching the availability and lead time on components at the design stage can reduce the risk of supply chain challenges later down the line.
In short, start planning supply needs now. Getting started early is the best way to avoid any delays in production. Partnering with a collaborative supplier that can solve both design and supply challenges could be crucial in keeping your production line running.
At TFC, we usually work anywhere from eight to 12 months ahead to avoid any delays in shipments, but the most important thing for us is that we’re honest and upfront about the challenges the industry is facing. These issues aren’t going anywhere anytime soon, so staying ahead of shortages and identifying design flaws early on is the best way forward
TFC has been a leading supplier of engineering products for over 60 years, supporting with design development, high quality components and tailored inventory solutions. For more information, contact Simon Ward at SWard@tfc.eu.com
Latest News From TFC
Catch up on all of the latest supply chain, fastener industry and company news from TFC Ltd.
Catch up on all of the latest supply chain, fastener industry and company news from TFC Ltd.