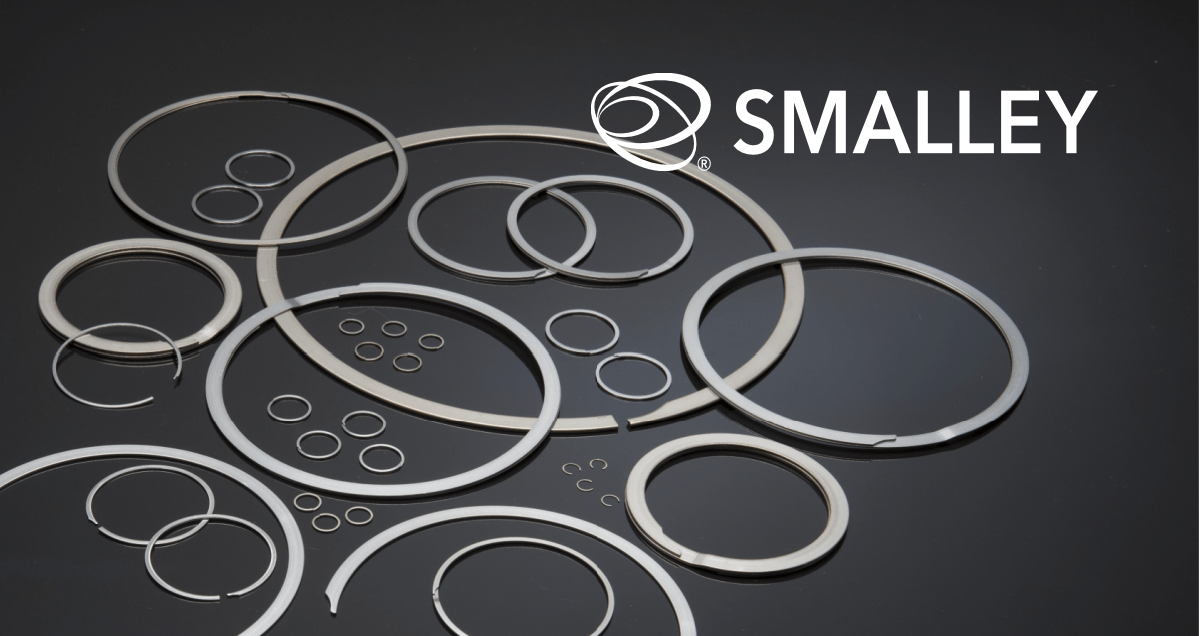
Customer Challenge
A manufacturer of medical devices had plans to design a new anaesthesia machine used to ventilate patients with endotracheal tubes or supraglottic airways in place during general anaesthesia.
During prototyping, they tried using a conventional DIN 7993 round wire snap ring in the valve body. However, during the first test phases, it turned out that the ring’s residual burrs caused damage to the rubber coating in the valve. The damaged valve wall caused the ring to expand, twist and ultimately fall out.
TFC Solution
To solve the problem, TFC proposed a multiple-turn Smalley Spirolox retaining ring.
Smalley retaining rings are made by edgewinding, resulting in a circumferential grain structure, giving exceptional strength, dimensional stability, and a burr-free yet flexible solution. Before edgewinding, the round wire is processed through a rolling mill to achieve a flat state. The edgewinding process then takes the flat wire and coils it on edge. The result was a retaining ring with a smooth radius edge, which was required in this application, ensuring the valve’s rubber coating remained undamaged.
A further benefit of the edgewinding process is zero tooling costs, so whether it’s a prototype or production run, modifications can quickly and easily be made during any stage of the process, so custom rings get delivered fast and with No-Tooling-Cost™. This method also ensures that the production product is identical to the prototype for worry-free manufacturing.
Since the ring was to be used in a medical device, the material chosen was AISI 316. Due to its molybdenum content, the material has a very high temperature and corrosion resistance. Furthermore, the surface is vapour degreased and ultrasonically cleaned. Thus, the material and the surface treatment fitted precisely into our client’s requirements and differed significantly from standard alloys of conventional stamped circlips.
Result
Thanks to the Smalley retaining ring’s unique properties, the customer could guarantee the process reliability of the valve and successfully launch the product to market.
Request FREE Samples
Request free samples of any of our standard parts to test in your application, or leave the specific part blank, and we will send you a sample box.
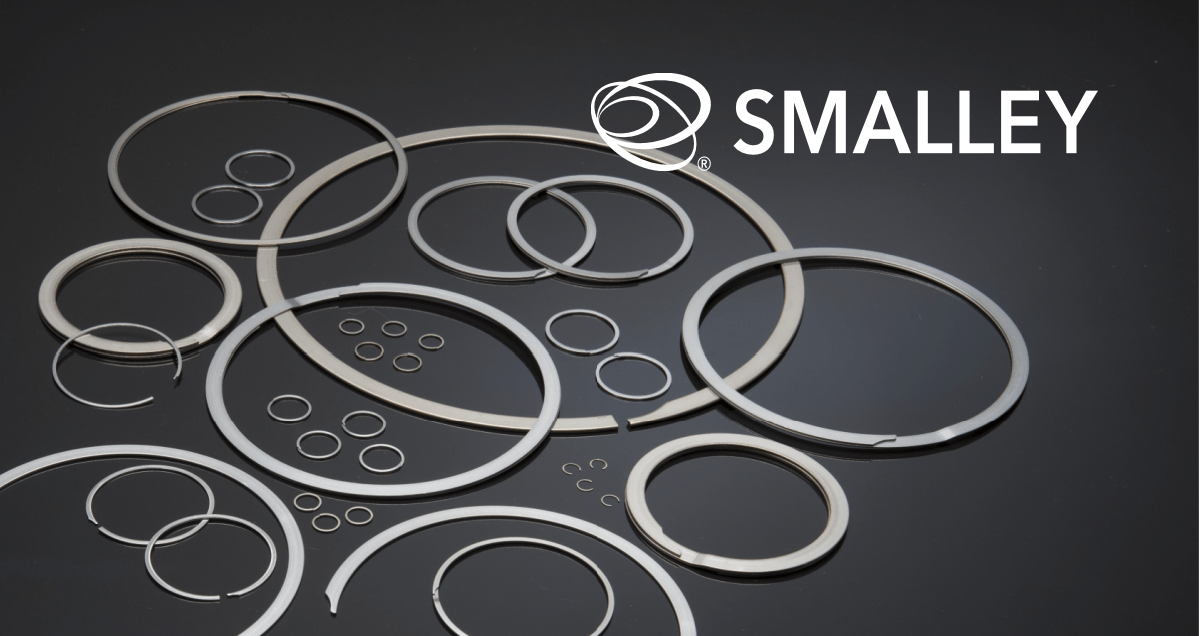
Customer Challenge
A manufacturer of medical devices had plans to design a new anaesthesia machine used to ventilate patients with endotracheal tubes or supraglottic airways in place during general anaesthesia.
During prototyping, they tried using a conventional DIN 7993 round wire snap ring in the valve body. However, during the first test phases, it turned out that the ring’s residual burrs caused damage to the rubber coating in the valve. The damaged valve wall caused the ring to expand, twist and ultimately fall out.
TFC Solution
To solve the problem, TFC proposed a multiple-turn Smalley Spirolox retaining ring.
Smalley retaining rings are made by edgewinding, resulting in a circumferential grain structure, giving exceptional strength, dimensional stability, and a burr-free yet flexible solution. Before edgewinding, the round wire is processed through a rolling mill to achieve a flat state. The edgewinding process then takes the flat wire and coils it on edge. The result was a retaining ring with a smooth radius edge, which was required in this application, ensuring the valve’s rubber coating remained undamaged.
A further benefit of the edgewinding process is zero tooling costs, so whether it’s a prototype or production run, modifications can quickly and easily be made during any stage of the process, so custom rings get delivered fast and with No-Tooling-Cost™. This method also ensures that the production product is identical to the prototype for worry-free manufacturing.
Since the ring was to be used in a medical device, the material chosen was AISI 316. Due to its molybdenum content, the material has a very high temperature and corrosion resistance. Furthermore, the surface is vapour degreased and ultrasonically cleaned. Thus, the material and the surface treatment fitted precisely into our client’s requirements and differed significantly from standard alloys of conventional stamped circlips.
Result
Thanks to the Smalley retaining ring’s unique properties, the customer could guarantee the process reliability of the valve and successfully launch the product to market.
Request FREE Samples
Request free samples of any of our standard parts to test in your application, or leave the specific part blank, and we will send you a sample box.
Latest Case Studies From TFC
Catch up on all of the latest case studies from TFC Ltd.
Latest Case Studies From TFC
Catch up on all of the latest case studies from TFC Ltd.
Get Social